The degradation of materials is a process that leads to change in their properties due to environmental effects.
All materials, whether plastics, organic materials, ceramics, metals, or composite materials, degrade at a varying rate. The speed at which they deteriorate depends on the wear and tear caused by repeated constraints, but also on the environment in which they are found. For example, exposure to certain chemicals, ultraviolet radiation, or the effects of freezing and thawing can degrade certain materials. Their initial properties are then modified by the effects of the ambient environment.
Exposure to oxygen and water causes the structure of a bridge to rust.
Ultraviolet rays cause degradation of the plastic.
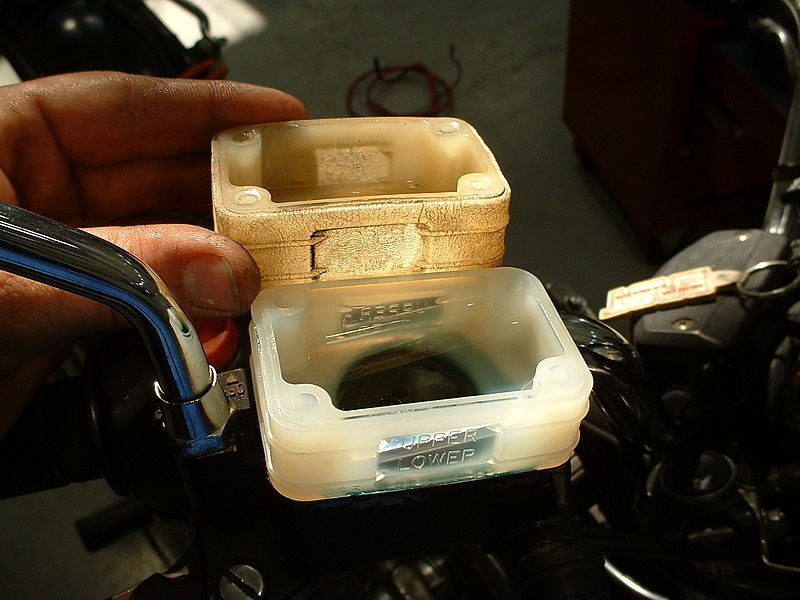
The protection of materials consists of using processes and treatments to slow down or prevent their degradation.
If nothing is done to counter the harmful effects of the environment on a material, it will degrade faster than if it were to wear out from constraints alone and will ultimately be destroyed. There are ways to minimize or delay the degradation of materials. Depending on the ambient environment and the type of material considered, appropriate protection techniques must be chosen.
The degradation and protection processes specific to each type of material are discussed in the concept sheets dealing with the various categories of materials.
The heat treatment of alloys is a process that modifies the mechanical properties of the alloy by subjecting it to heating cycles.
Heat treatments, although they can be performed on wood and glass, are usually carried out on alloys. These treatments require high temperature heating. The purpose of heat treatments is to rearrange the molecules of an alloy by heating it to modify its mechanical properties. Indeed, the new arrangement of the molecules obtained restores the mechanical properties of the alloy in the case of a repair or provides new ones in the case of a modification.
The three main heat treatments of alloys are quenching, tempering, and annealing.
- Quenching improves the hardness of mechanical parts, while making them a little more brittle. This treatment consists of two stages. The alloy must first be heated to a very high temperature so that the atoms can be rearranged. The alloy is then cooled very quickly, by soaking it in a cold fluid. This quenching interrupts the motion of atoms and provides the alloy with new properties.
- Tempering makes an alloy a little more ductile, while allowing it to retain a certain hardness. This treatment is carried out on an alloy that has already been quenched. It consists in heating a quenched alloy to a precise temperature, lower than the quenching temperature so that the alloy does not lose the properties acquired during this stage. The higher the tempering temperature, the less hard and more ductile it will be.
- Annealing restores the properties of the alloy after its deformation. To do this, the alloy must be heated sufficiently and then slowly cooled thereafter. It is then possible to erase the traces left by constraints during the manufacturing process, such as traces of welding. Alloys can also be made softer and easier to machine.